What Do You need to Know about Robotic Picking System Warehouse?
Order fulfillment in warehouses encompasses numerous routine activities, with order picking standing out as the cornerstone. Typically, this process is a major cost driver in distribution centers, accounting for a substantial portion of the total operational expenditure.
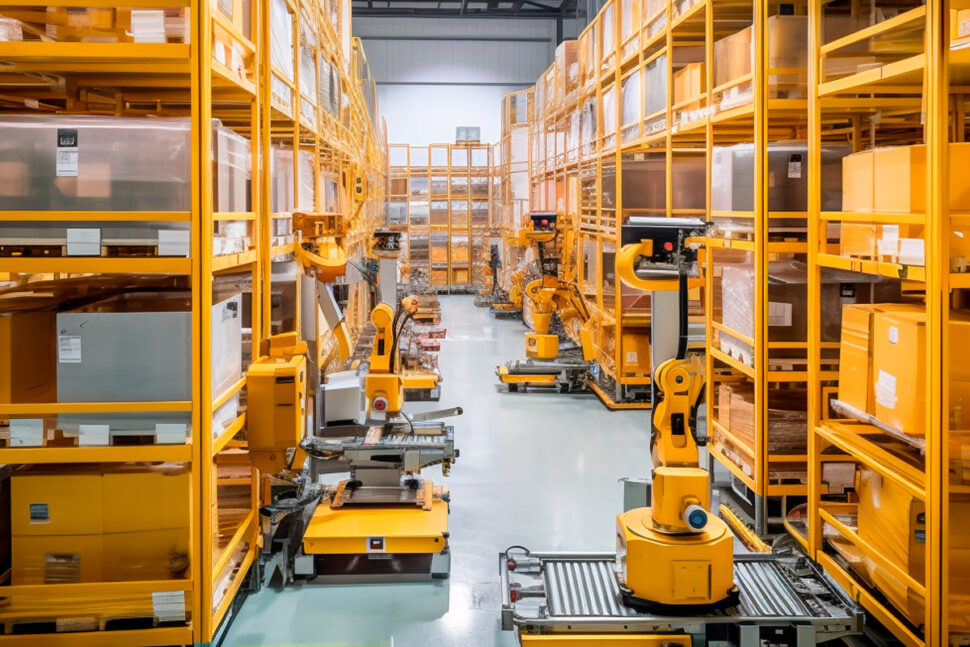
Therefore, gaining insights into various robotic picking systems is imperative to enhance the functionality of your distribution hub. Leveraging suitable fulfillment technologies can amplify productivity, reduce downtime, slash expenses, and expedite order dispatch timelines. Efficient robotic tools coupled with cutting-edge picking methodologies can pave the way for peak operational performance, satisfied customers, and elevated levels of loyalty and retention.
What Does “Order Picking” Mean?
Order picking refers to the act of selecting products from a warehouse’s stock to satisfy customer orders, typically stemming from online shopping. It stands as a foundational element of warehouse operations, often being the most time-consuming and costly phase of order fulfillment. In the past, this task primarily relied on individuals navigating extensive warehouse rows to gather products, which were then taken to the packaging area for dispatch to buyers.
Today’s consumers anticipate swift delivery schedules, even for orders with multiple SKUs, delivered straight to their doorsteps. Recognizing the significance of order picking in terms of expenses, operational effectiveness, and precision, companies are gravitating towards innovative robotic solutions to enhance efficiency. The integration of robotic picking strategies not only expedites the picking duration but also reduces downtime, ensuring service level agreements are consistently achieved.
What Exactly Are Robotic Picking Systems?
At its core, a robotic picking system refers to an automated order fulfillment solution that integrates robots and warehouse management software, streamlining portions or the entirety of the picking procedure within an online retail warehouse.
Such robotic mechanisms collaborate seamlessly with warehouse personnel. By handling mundane and repetitive chores that might cause fatigue, they allow your team to concentrate on tasks of greater significance.
Types of Robotic Picking Systems
Robotic picking systems are revolutionizing warehouse operations by offering automation solutions for a traditionally labor-intensive process. There are several types of robotic picking systems, each designed to cater to specific needs and scenarios. Here are some of the primary types:
- Goods-to-Person (GTP) Systems: Robots bring the required goods or storage bins to the worker. This eliminates the need for workers to walk through the aisles, improving efficiency.
- Piece Picking Robots: These robots use a combination of cameras, sensors, and grippers to pick individual items from bins or shelves. Advanced models incorporate AI and machine learning to adapt and improve their picking techniques over time.
- Autonomous Mobile Robots (AMRs): These are self-navigating robots that can transport items within the warehouse, either assisting in the picking process or moving goods from picking to packing or shipping zones.
- Robotic Arms: Traditional robotic arms, often equipped with various end effectors, can pick, pack, and even palletize goods. With advances in AI and machine vision, these arms can handle a diverse range of items and tasks.
- Collaborative Robots (Cobots): These are designed to work safely alongside humans. They often have built-in safety features to ensure they stop or slow down when close to a human operator.
- Zone Picking Robots: In this system, robots are responsible for specific zones within a warehouse. When an order requires items from different zones, robots collaborate to complete the order, passing items between zones if necessary.
- Tote Retrieval Robots: These robots focus on retrieving entire totes or bins of products, rather than individual items. They’re especially useful for bulk order processing.
- 3D Vision Robots: These robots use advanced 3D vision systems to identify, locate, and pick items, even if they’re buried under other products.
- Vacuum or Suction Grippers: Robots equipped with suction technology can pick up a wide range of products, especially those with flat surfaces. This is especially useful for items that might be delicate or challenging for traditional grippers.
- Shelving and Restocking Robots: While their primary role isn’t picking, these robots assist in the process by ensuring items are restocked and available for pickers (human or robotic).
In choosing the right robotic picking system, it’s crucial to consider the specific requirements of the warehouse, the nature of the items being handled, order volumes, and the desired level of automation. As technology advances, it’s likely we’ll see even more specialized robotic systems designed for various niches within the warehousing and logistics industries.
Some conclusion
Robotic picking systems present a diverse range of options, each tailored to optimize various facets of the warehousing process. When appropriately chosen and implemented, these systems can drastically enhance productivity, reduce unnecessary downtime, decrease operational expenses, and elevate the overall satisfaction of your customers. Optimal systems strategically reduce the need for manual warehouse navigation and streamline interactions between humans and robots, ensuring a smooth and efficient workflow.
The Goods-to-Person automation, in particular, stands out as a game-changer for third-party logistics (3PL) warehouse managers and e-commerce enterprises. It addresses crucial performance indicators such as expediting order fulfillment, dramatically enhancing pick rates, and curtailing non-productive time. Moreover, it promises amplified overall productivity. For those wary of massive capital expenditure (CapEx) or extensive infrastructural overhauls, mobile robotic systems serve as an excellent choice. Not only are they more cost-effective, but they also offer the flexibility to adapt to dynamic warehousing environments, making them a future-proof investment.
Sources:
- https://www.tractica.com/research/warehouse-robotics/
- https://www.logistics.dhl/global-en/home/insights-and-innovation/insights/robotics-in-logistics.html
- IEEE Spectrum: Inside the Robot-Run Warehouse of Tomorrow
- https://www.mckinsey.com/business-functions/operations/our-insights/automation-robotics-and-the-factory-of-the-future
- https://www.weforum.org/agenda/2021/05/technology-trends-warehouse-automation/
- https://www.aboutamazon.com/news/innovation-at-amazon/amazon-robotics
Watch our Podcast
Get a quote in minutes!

GUIDE TO AVOID UNNECESSARY FREIGHT CHARGES
This is the A-to-Z guide of accessorial charges... it includes an explanation of each fee, the standard industry rates, as well as tips on how to handle them like a pro.
Just enter in your email address and receive your FREE E-Book in minutes!
Recent Posts
- Top 8 Best Warehouses in Miami 08/27/2024
- Top 10 Top-Tier Bonded Warehouses in Miami 08/08/2024
- Essential Insights: All You Have To Know About Pharmaceutical Warehousing 08/01/2024
- E-Commerce Freight Forwarding: A Simple Overview 08/25/2023
- What Do You need to Know about Robotic Picking System Warehouse? 08/24/2023
- Cross-Docking vs. Warehousing: Navigating the Intricacies of Miami Logistics 08/18/2023
- The Future of Storage: How Modular Warehouses Can Help Business Operations? 08/15/2023
- Transloading vs. Cross-docking: Key Differences in Logistics 08/11/2023
- Transloading in Logistics: Understanding the Process and Meaning 08/11/2023
- The Key Differences between Warehouses and Fulfillment Centers in E-commerce 08/04/2023